Machine Foundation Analysis and Design
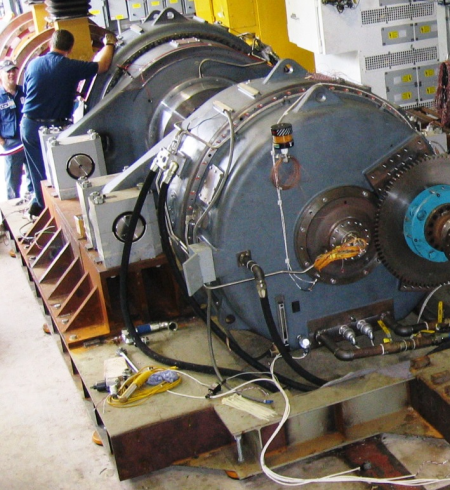
Description
1 GENERAL DESIGN REQUIREMENTS
2 FOUNDATIONS AND STRUCTURES FOR VIBRATING MACHINERY
2.1 Scope
2.2 Definitions
2.3 Design criteria for all heavy machinery
2.4 Design criteria for reciprocating machinery
2.5 Design criteria for rotary machinery
2.6 Design criteria of light vibrating machinery
3 LOADING OF MACHINE FOUNDATIONS
3.1 Static loads
3.2 Rotating machine loads
3.3 Reciprocating machine loads
3.4 Impulsive machine loads
3.5 Loading conditions
3.4 Impulsive machine loads
3.5 Loading conditions
Calculation Reference
Design for Machine Vibration
FOUNDATIONS AND STRUCTURES FOR VIBRATING MACHINERY
Rotating machine loads
Foundations and structures for vibrating machinery are designed to support heavy machinery that generates vibrations during operation. These vibrations can cause structural damage, negatively impact the performance of the machinery, and transmit vibrations to nearby structures or the surrounding environment. To minimize these issues, special considerations must be taken into account when designing foundations and structures for vibrating machinery.
Some key aspects to consider when designing foundations and structures for vibrating machinery include:
-
Isolation: The foundation should be designed to isolate the vibrating machinery from the rest of the structure or adjacent structures. This can be achieved using various techniques, such as using isolators or pads made from materials that absorb vibrations, creating gaps between the machinery foundation and the surrounding structure, or constructing the foundation on a separate, isolated slab.
-
Mass: The mass of the foundation should be sufficiently large to ensure stability and minimize the transmission of vibrations. A general rule of thumb is that the mass of the foundation should be 3 to 5 times the mass of the supported machinery. However, this ratio may vary depending on the specific machinery, soil conditions, and other factors.
-
Stiffness: The foundation should be designed to have a high stiffness to prevent excessive deformation and movement under the dynamic loads generated by the machinery. This can be achieved by using reinforced concrete or other rigid materials and designing the foundation with appropriate dimensions and reinforcement.
-
Damping: Damping is the ability of the foundation to dissipate the energy of vibrations. The foundation should be designed to provide adequate damping, either through the use of materials with inherent damping properties or by incorporating external damping devices, such as dampers or tuned mass dampers.
-
Natural frequency: The natural frequency of the foundation and the supported structure should be considered during design. Ideally, the natural frequency of the foundation should be different from the dominant frequencies of the vibrating machinery to avoid resonance, which can amplify vibrations and cause structural damage.
-
Soil properties: The properties of the soil, such as its bearing capacity, shear strength, and stiffness, must be considered when designing the foundation. The soil should be capable of supporting the combined static and dynamic loads generated by the machinery and the foundation. A geotechnical investigation may be necessary to determine the soil properties and select the appropriate foundation type, such as shallow or deep foundations.
-
Maintenance and monitoring: The foundation should be designed with access for maintenance and monitoring of the machinery, as well as the foundation itself. Vibration sensors and other monitoring equipment may be installed to assess the performance of the foundation and identify potential issues.
Designing foundations and structures for vibrating machinery requires a thorough understanding of the dynamic behavior of the machinery, the foundation, and the supporting soil. Various standards and guidelines, such as the International Building Code (IBC) or the American Concrete Institute (ACI) 351, provide recommendations for designing foundations and structures for vibrating machinery. Engineers should also consult the manufacturer's recommendations and consider any site-specific conditions when designing the foundation.
Calculation Preview
Full download access to any calculation is available to users with a paid or awarded subscription (XLC Pro).
Subscriptions are free to contributors to the site, alternatively they can be purchased.
Click here for information on subscriptions.