Bolts and Threads
0 ContainersFiles in Bolts and Threads
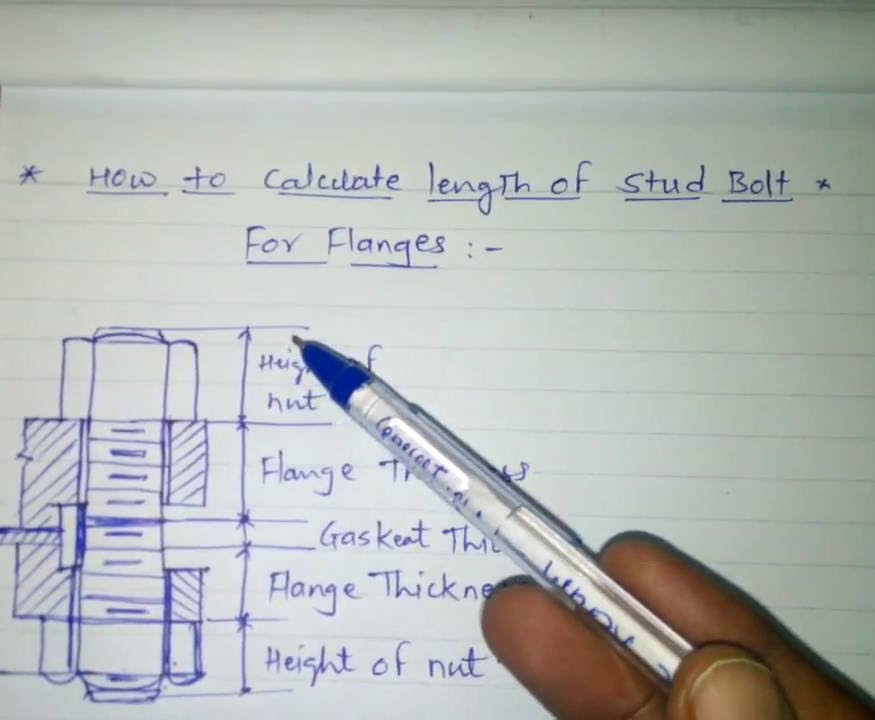
Bolt length calculator
Given the clamping thickness, the bolt length would be calculated
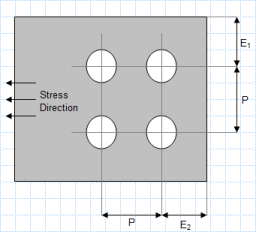
Bolt spacing and edge distances.xls
The minimum and maximum fastener spacing, end distances, and edge distances for steel plates are t...
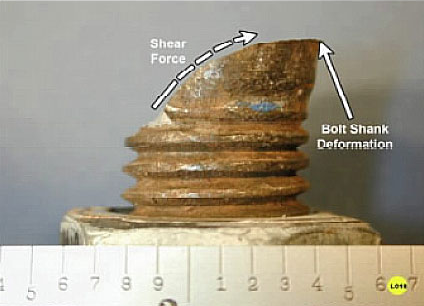
Bolt Stress MIL-HDBK-5
Calculates the allowable pre-load after a user input shear load or the allowable shear load after a user input pre-load for coa...

BoltedJoint.xls
To determine the force distribution in a preloaded bolted joint, you can follow these steps:
Understand the Joint Configuration...
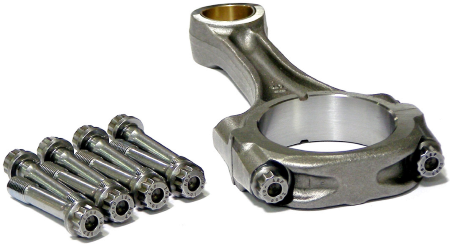
Connecting Rod Bolts Calculation with VDI 2230 standards
I have calculated the Connecting rod bolt analysis with VDI 2230 standards.I still think I have made so many mistakes.Ple...
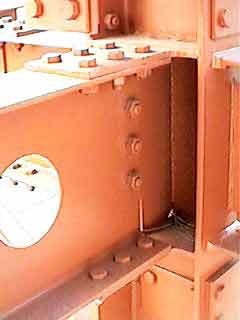
Eccentric Loaded Bolted Joint
Enter bolt locations, applied load and location of load. Calculates bolt shear, tension, etc. I use this all the time at work and it ma...
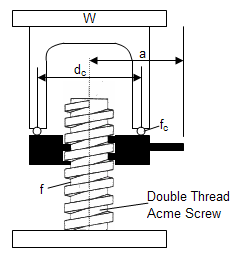
Power screw calculations.xls
KNOWN: A double thread Acme screw and a thrust collar, each with known diameter and running friction coefficient, are used to raise a speci...
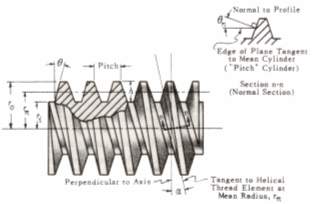
Power Screw.xls
Purpose of calculation: For an applied load on a screw thread calculate the axial thrust of a nut. Calculate bolt pretension from screw parameter...
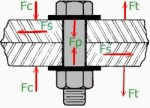
Quick and Dirty Bolt Sizing Calculation.xls
https://www.youtube.com/watch?v=x5G5xPAt5To
The following values are required as inputs to the calculation:
- BOLT GRADE - Enter the two num...
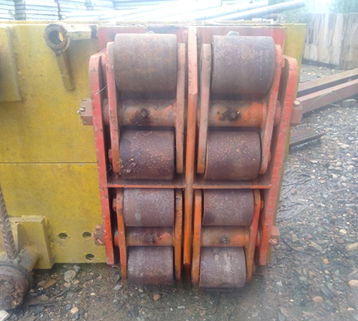
Steel Roller Structural Analysis
AMERICAN INSTITUTE OF STEEL CONSTRUCTION, INC. (AISC)
Specification for Structural Steel Buildings
Allowable Stress Design and Plastic Design
...
