ExcelCalcs :: File Repository
RSS
Bolts and Threads
RSS


0 33
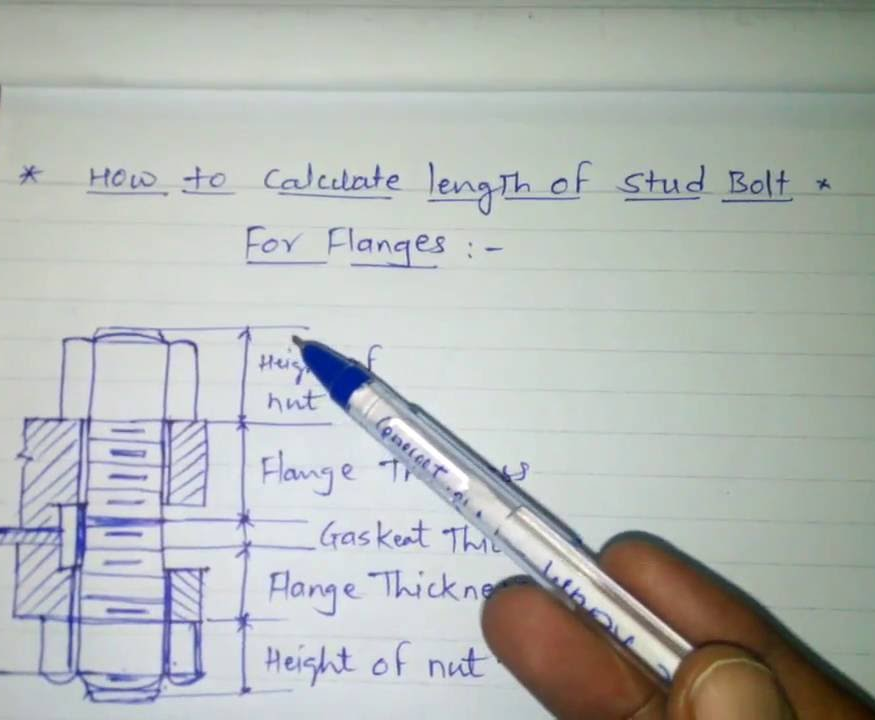
Bolt length calculator
Short Description:
Given the clamping thickness, the bolt length would be calculated
Submitted By:
Last Modified
15 May 2020
Downloads:
42
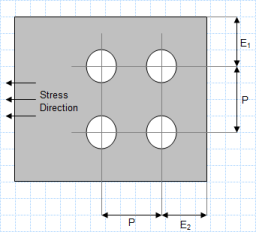
Bolt spacing and edge distances.xls
Short Description:
The minimum and maximum fastener spacing, end distances, and edge distances for steel plates are t...
Submitted By:
Last Modified
19 Jul 2023
Downloads:
1196
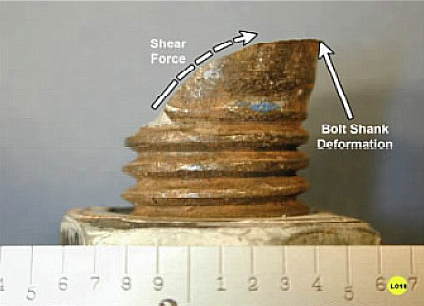
Bolt Stress MIL-HDBK-5
Short Description:
Calculates the allowable pre-load after a user input shear load or the allowable shear load after a user input pre-load for coa...
Submitted By:
Last Modified
19 Jul 2023
Downloads:
111
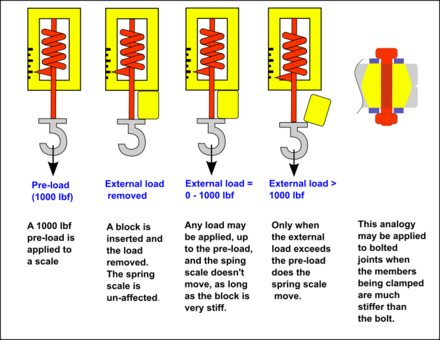
BoltedJoint.xls
Short Description:
To determine the force distribution in a preloaded bolted joint, you can follow these steps:
Understand the Joint Configuration...
Submitted By:
Last Modified
19 Jul 2023
Downloads:
850
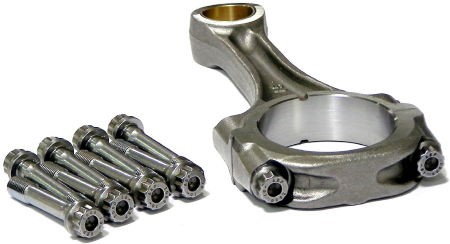
Connecting Rod Bolts Calculation with VDI 2230 standards
Short Description:
I have calculated the Connecting rod bolt analysis with VDI 2230 standards.I still think I have made so many mistakes.Ple...
Submitted By:
Last Modified
19 Jul 2023
Downloads:
57
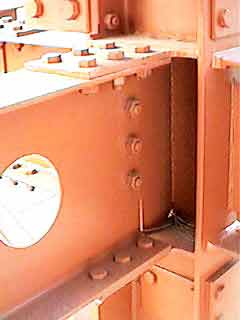
Eccentric Loaded Bolted Joint
Short Description:
Enter bolt locations, applied load and location of load. Calculates bolt shear, tension, etc. I use this all the time at work and it ma...
Submitted By:
Last Modified
19 Jul 2023
Downloads:
170
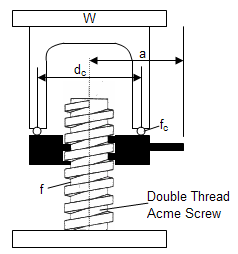
Power screw calculations.xls
Short Description:
KNOWN: A double thread Acme screw and a thrust collar, each with known diameter and running friction coefficient, are used to raise a speci...
Submitted By:
Last Modified
19 Jul 2023
Downloads:
377
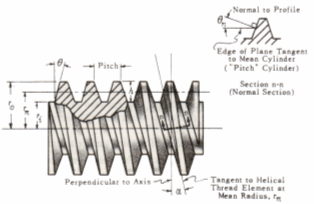
Power Screw.xls
Short Description:
Purpose of calculation: For an applied load on a screw thread calculate the axial thrust of a nut. Calculate bolt pretension from screw parameter...
Submitted By:
Last Modified
19 Jul 2023
Downloads:
509
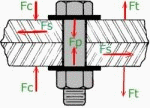
Quick and Dirty Bolt Sizing Calculation.xls
Short Description:
https://www.youtube.com/watch?v=x5G5xPAt5To
The following values are required as inputs to the calculation:
1) BOLT GRADE - Enter the two num...
Submitted By:
Last Modified
16 Jan 2020
Downloads:
666
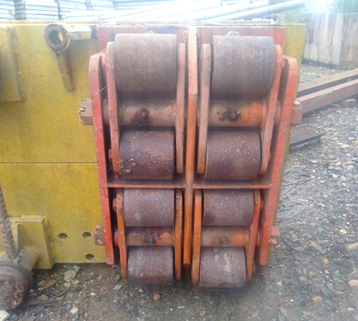
Steel Roller Structural Analysis
Short Description:
AMERICAN INSTITUTE OF STEEL CONSTRUCTION, INC. (AISC)
Specification for Structural Steel Buildings
Allowable Stress Design and Plastic Design
...
Submitted By:
Last Modified
17 Mar 2021
Downloads:
14