Fracture Mechanics
If a component is
subject to repeated applications of structural loading then it will be
susceptible to fatigue failure. Stresses act on small flaws inherent
in the material causing then to grow until they break. Two approaches
can be employed to assess this situation:
• Fatigue Life Assessment.
• Fracture Mechanics Approach.
Using stress information derived from an ANSYS structural analysis
MoreVision have developed custom programs to assess fatigue life or to
study crack growth.
Our library of programs includes methods of assessment used in various
countries following a number of codes:
Fatigue Life Assessment
• UK - BS7608 (fabricated steel), BS8118 (aluminium), BS5400
(bridges), BS2573 (cranes).
• US - AISC LRFD.
• France - UIC 515-4 Goodman Diagram (railway).
• German DIN 15 018 (cranes).
• Swedish Volvo standards (automotive, construction
equipment).
Fracture Mechanics Approach
• UK - PD6493 (fracture).
The fatigue life
of a welded structure it totally dependant upon the choice of welded
detail. In the following examples the detail on the left hand side
of the page is improved by adopting the detail on the right hand side.
Just three examples are given though there are generally many ways of
optimising a fabricated structure.
1) Weld reinforcement and weld toe re- profiling
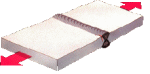
The fatigue life of this butt weld is improved by grinding the weld
reinforcement flush with the parent plate. This reduces the stress
concentration at the weld toe. Paradoxically it could be further
enhanced if the weld toes are dressed back 1 to 2mm below the
thickness of the parent plate! The benefit from the removal of poor
quality material at weld toes which contains fatigue prone inherent
flaws outweighs the slight increase in stress due to loss of net
section.
2) Removal of weld stop starts
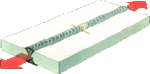
The
presence of stop start defects in a weld will reduce the fatigue life
of a weld.
3) Do not weld on plate edges
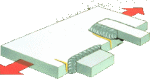
Welds
on the edge of a stressed plate have a lower fatigue life than welds
which stop 10mm short of the edge.
|
Consultancy Projects - Fatigue Analysis Of Welded structures
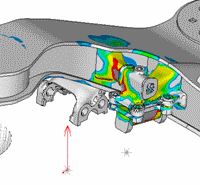
Finite element stress analysis.
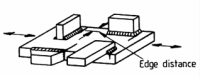
Understand fatigue classification of welds.
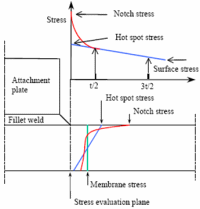
Understand how to select appropriate stress from finite element model for fatigue assessment.
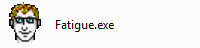
Software developed by MoreVision to take benefit from fatigue
enhancement methods (like toe grinding, TIG dressing and stress
relieving).
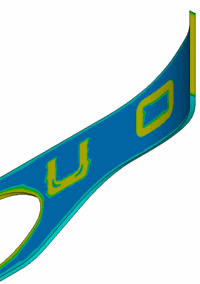
View fatigue classification directly on finite element model.
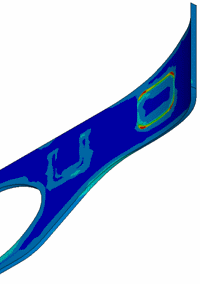
View damage directly on finite element model.
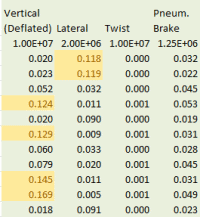
Export results to spreadsheet for detailed analysis and verification.
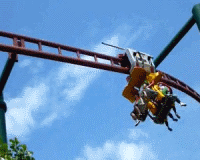
Fatigue assessment of rollercoasters.
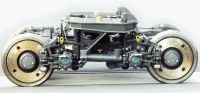
Fatigue assessment of railway bodyshells and running gear.
|