Honeycomb Beam & Panel Calculations
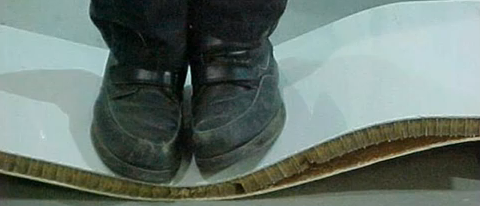
Description
This spreadsheet has been developed to allow design engineers to quickly size honeycomb panels with a minimum of work. The calculation is driven from 'Home' worksheet using a simple 5 step process.
1) SELECT Core material from drop down box:2) SELECT skin material from drop down box:
3) SELECT Panel Loading condition from drop down box:
? Beam, Simple Support with Uniform Load Distribution
? Beam, Both Ends Fixed with Uniform Load Distribution
? Beam, Simple Support with Central Load
? Beam, Both Ends Fixed with Central Load
? Beam, Cantilever with Uniform Load Distribution
? Beam, Cantilever with Load at End
? Rectangular plate, simply supported, uniform load.
? Rectangular plate, clamped, uniform load.
? Rectangular plate, simply supported, concentrate load over small area
? Rectangular plate, clamped, concentrate load over small area
? Circular plate, simply supported under uniform distributed load
? Circular plate, clamped under uniform distributed load
? Circular plate, simply supported under central force
? Circular plate, clamped under central force
4) INPUT Panel dimensions and total load
5) READ Results - Green ticks indicate an acceptable result. Red crosses indicate an unacceptable result.
Although it is only necessary to use the 'Home' worksheet all supporting data and detailed calculations are given on other worksheets.
Calculation Reference
Honeycomb Panel Design
Composite Panel Design
Designing with Lightweight Materials
Calculation Preview
Full download access to any calculation is available to users with a paid or awarded subscription (XLC Pro).
Subscriptions are free to contributors to the site, alternatively they can be purchased.
Click here for information on subscriptions.
Comments: 7
×
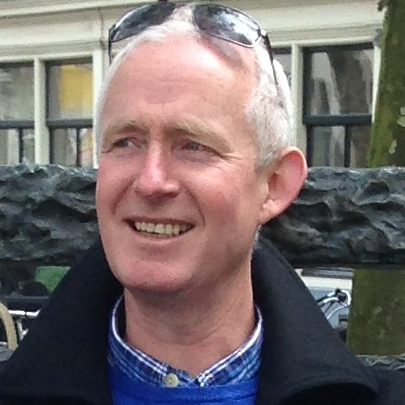
johndoyle-admin
3 years ago
See [this page](/pricing/compare-subscription-plans/)
3 years ago
Hi, John how does one download this file I have registered but don't see a download button for this file like on other pages neil@uk-esc.com
6 years ago
Hello John,
I recently ran across a problem where the honeycomb panel was composed of different upper and lower face sheet thicknesses, for instance, upper face sheet was 1.27mm lower face sheet was .635mm. The upper face will be in compression whilst the lower is in tension. To create a minimum weight panel the face sheets were optimized. This occurs on Embraer floor panels. This creates a bit of an analysis challenge. Can you offer a suggestion?
Cheers,
Tom
I recently ran across a problem where the honeycomb panel was composed of different upper and lower face sheet thicknesses, for instance, upper face sheet was 1.27mm lower face sheet was .635mm. The upper face will be in compression whilst the lower is in tension. To create a minimum weight panel the face sheets were optimized. This occurs on Embraer floor panels. This creates a bit of an analysis challenge. Can you offer a suggestion?
Cheers,
Tom
9 years ago
You are correct T181 I afraid there is an error in the core shear stress for cases 11 and 12. I will make the correction and upload a new version. Thanks for reporting this in :)